Abrasive Blasting and Surface Preparation Methods
IPCQ have extensive experience in abrasive blasting surface preparation using a range of blast media including steel grit, sponge and Australian GMA Garnet.
With over 45 years of experience, IPCQ have the expertise to offer a range of Abrasive Blasting services including traditional and automated systems utilising a variety of blast media’s ranging from garnet, steel grit and Steel shot. In 2011 IPCQ imported the first “Faster Blaster” to Australia. This innovative machine enables IPCQ to complete large projects in the shortest time and the safest way possible.
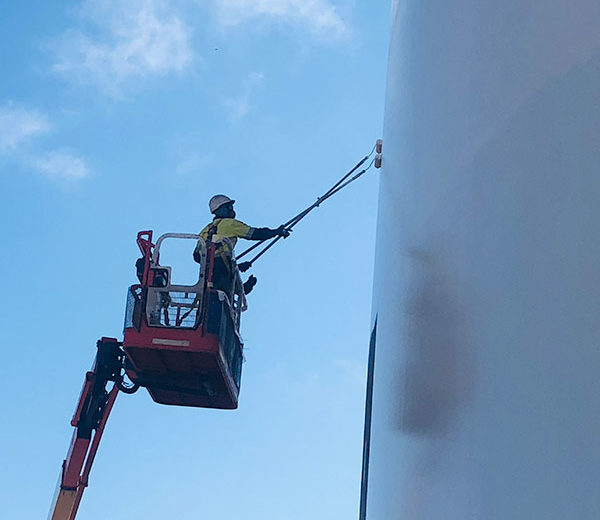
Abrasive Blasting and Surface preparation methods
We specialise in the following abrasive blasting and painting and surface preparation methods
Abrasive Blasting and Surface preparation methods
IPCQ have pioneered the use of automated surface preparation units within Australia. The technology utilises steel grit/shot in lieu of traditional blast media and eliminates the requirement for substantial and expensive clean-up and waste disposal processes. The machine forms a firm seal on the substrate preventing emissions from being released which also often allows for simultaneous operations to occur. The abrasive material is fully recoverable and recyclable which significantly reduces the amount of regulated waste generated. Our system is fully contained so environmental impacts are mitigated or often eliminated completely.
The technology has the ability to abrasive blast both horizontally and vertically while containing the air born particles usually associated with surface preparation. This method has been proven invaluable when managing debris deriving from lead containing paint.
What is vapour abrasive blasting?
Wet abrasive blasting (also known as vapour abrasive blasting) removes coatings, contaminants, corrosion and residues from several substrate types. It’s similar to dry blasting, except that the blast media is moistened prior to impacting the surface, this reduces the dust generated by 60%. It also reduces the amount of abrasive that is spent by 40%, meaning less waste and less clean-up. Vapour blasting can also reduce the need for full containment without compromising on environmental controls.
IPCQ has the means to complete projects both on site and within a shop environment including the design and construction of on site blast and paint facilities. Recently IPCQ installed a state of the art, purpose built blast and paint facility on client premises. IPCQ operated this facility to successfully deliver over 33,000 meters of spool work.
For traditional Dry Abrasive Blasting activities, IPCQ typically utilises a blast media that is classified as a non-hazardous, non-dangerous good that is a naturally occurring mineral with no known ecotoxicity. The product is insoluble in water and unlikely to contaminate waterways or food chains. Anecdotal information from blasting operators is that this Australian-mined GMA garnet produces minimal dust compared to some other courser grades and sources of garnet. We have specialised vacuum equipment that can be adapted to ensure no dust or abrasive can escape to the atmosphere. This technique is great for smaller projects where the cost of containment maybe a burden.